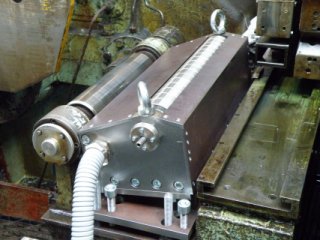
In the production of metal sheets on rolling mills, it is necessary to measure several parameters of metal sheets so that it is possible to affect the quality of the product in real time. Because of the inhomogeneity of used material, imperfect shape, thermally and otherwise unstable rolling conditions, uneven tensile strain distribution occurs in different parts of the sheet in the real metal sheet rolling process. This is manifested by thickness fluctuations at various points on the sheet, by corrugated parts of sheet or by sheet running sideways. These effects adversely affect the final quality of the produced metal sheet and it is therefore important to eliminate them during production. The correction process can be performed by adjusting the parameters of rolling stand. This allows to adjust spacing of the rolls (and thus the thickness of metal sheet) and also the tilting and bending of rolls so that conditions in different parts of the sheet can be different to offset differences in a specific places. Measure data from tensile strain distribution can also be used as input parameters for setting rolling stand. Metal sheet is guided over the measuring cylinder with a small wrap angle and thus applies force on the cylinder. The cylinder consist of several segments, which makes it possible to measure the force from the metal sheet. The force applied by individual segment is measured using strain gauges (tensometric force sensors). Robust design of these strain gauges is compatible with steel industry. From the measured force along the measuring cylinder (perpendicular to the metal sheet) is possible to derive requirements for the correction of the setting of rolling stand.